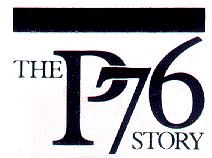
September 1975 and the only eight Force 7Vs ain captivity" go under the
auctioneer's hammer. The Vs were V8powered
Why it sank
People love to laugh about the P76 these days, but was it the lemon everyone seems to
think? Geoffrey Bewley sets the records straight
IN THE early 70s the Leyland P76 transited the Australian motoring scene like a meteor There was the
same sort of initial flash, blaze of brilliant light and swift plunge into darkness. Few
new cars can ever have won more applause. But inside two years, Leyland Australia was in
retreat, the P76 coupe
and station wagon versions were aborted and the P76 was stone dead.
The Leyland management had known they were taking a risk with the P76 project. Ventures into the
family car field by Leyland's forebears hadn't been terribly successful This time they
studied past errors, planned carefully to avoid repeating them and tackled the technical
side thoroughly and from a fresh angle. They wanted to build a car that would surpass its
opposition, not just match it, and to a great extent they succeeded. But their reach
exceeded their grasp.
In the first place, it took decades of argument to convince a succession of parent
managements in England that big family cars were wanted out here. Australian motoring
wasn't at all like British motoring. Australians had to cover much greater distances over
much worse roads and they looked for big, strong cars to do it in.
Yes, the Morris Minor was a great little car. But it was a little car, and that put it
out of the picture as far as most Australian buyers were concerned. Warmed-over British
designs might dominate the small car market, but British car-makers could only increase
their share of the total market if they started building against Holden, Valiant and Ford.
One early shot, the Morris Marshall in 1958, was not a great success. A couple of years later a proposal for a
longer, wider and modified Austin Freeway was killed off on orders from England. In
1962 the local BMC management
set up a study group to see about building a genuine Australian BMC car. The groups
report recommended a large family model, powered by something like the new, light, alloy
V8 engine from the Buick division of General Motors.
But things had changed while the group was deliberating. The BMC Mini had become a
great success and more light, front-wheel drive designs from England were in the offing.
It seemed unnecessary to experiment with a large local design and the report was put
aside.
For some time it seemed that warmed over British designs were actually the ideal way to
go. But the later front-wheel drive models didn't do as well as BMC hoped and presently it
became clear that the company would have to build bigger cars after all if it were to make
any profits.
A new study group went to work in 1966. It came up with an ambitious plan for two new
model lines, with engine swaps providing a wide range of cars. There would be a V8 and a
slant four derived from it, and eventually a V12 and a slant six derived from that.
This was a terrific plan, but for technical and financial reasons it wasn't
practicable. So a scaled-down version was sketched out, still involving two production
lines, one for Model A light cars and the other for Model B family cars. Meanwhile, in
England BMC had merged with Leyland, so the Australian management had to win over a new
bunch of senior executives.
This time the parent company gave the thumbs up. It also provided plans of the
projected Leyland Marina for the Model A line in Australia. From farther up the corporate
sleeve they produced the superb 3.5-litre Rover alloy V8, based on the Buick engine
recommended by the 1962 study, to power the Model B car.
At first the Leyland engineers under David Beech thought in terms of another
front-wheel drive car and they tried a V8 in a modified Austin 1800. This was a technical
success, but it made the car too expensive to market in the Holden class. They decided on
a front-engined, rear wheel drive car instead and started drawing on a clean sheet.
In the early 70s the new car came together. The Rover engine was developed to a point
where it was almost a new design. The block was made deeper and stronger and the stroke
was lengthened to square so the pistons displaced 4.4 litres. It was fed by a Bendix
Stromberg two-barrel carburettor in place of the twin SUs used in Rovers. The power output
was said to be 161 kW.
Leyland stuck to the idea of offering a choice of engines. The alternative to the V8
was the six-cylinder unit from the Austin Tasman and Kimberley, enlarged from 2.25 to 2.6
litres. It kept up the percentage of local content and filled the gap while the Leyland
engineers produced a new Y6 based on the alloy V8.
The body design parameters were strength, simplicity, ease of maintenance and plenty of
passenger and luggage space. The styling was by Michelotti, with a wide, flat wedge shape
giving a low nose, deep hip-lines and a big, squared-off tail. There were fewer body parts
than usual for a car that size, which added strength and saved on welding time and cost.
Front suspension was by vertical struts and coil springs, with an anti-roll bar. Rear
suspension was by coil springs, a four-link live axle and telescopic dampers. Power brakes
were a standard fitting, working 27 cm discs forward and 23 cm by 3.8 cm drums aft.
Steering was by rack and pinion, with power steering for V8s.
Meanwhile, specifications and details had appeared in the motoring press. In February
1973, WHEELS had the first photos of P76 prototypes under test. Great things were expected
of the alloy V8 and it was claimed car thieves already had lists of clients seeking
examples to power 'specials' and boats. The body was praised for its clean, original
style. Light weight and excellent fuel economy were rumoured. A WHEELS editorial said the
new car was "keenly awaited".
The P76 was discussed in a big feature in the July WHEELS. "P76 is the most
important new car this year," it began. "For Leyland it is the most important
car in the company's history. It has cost $21 million and taken 500,000 miles of
development and five years to get into the showrooms."
The writers found the V8 gave plenty of power, as expected, and performance with the
six was surprisingly good. The steering was accurate and well-damped and the driver had a
good view out. The ride was good without much body roll. At high speed the car sat flat on
the road and felt very stable. There was some understeer, but it handled safely. Brakes
were good with plenty of feel.
The body was very roomy, with space for three adults across the back seat. There was
plenty of headroom. The boot was huge, with a low lip for easy loading. There wasn't much
wind noise, thanks to the smooth body. The tail was ugly and out of character with the
rest of the car.
Next month there was a full road-test report on a P76 Super, with a V8 and a four-speed
manual box. It confirmed the earlier good impressions. It was easy to drive, quick through
the gears, with light controls and very good brakes. The tall gear ratios took it to 170
km/h. Under test it did 6.0 km/l overall, and up to 7.1 km/l at cruising speeds. This was
regarded as disappointing; much better than the opposition's economy figures but not as
good as expected.
The totally new Leyland sedan emerged as a remarkably fine motor car said WHEELS
Boot and cabin space were commended again. There were second thoughts about the
driver's view; now it was classed as good ahead and to the sides and not so good to the
rear, thanks to the wedge shape. Noise level was generally good apart from some tyre
rumble.
Finish wasn't so good. The doors fitted badly and let water in. The instrument cluster
was loose, as was the centre console, and the steering wheel boss was coming away on one
edge. This was seen as okay in an early production car.
"If Leyland Australia can't sell the new P76 in profitable quantities, then there
is something wrong with the average new car buyer," WHEELS summed up. "It's that
simple. Once the assembly problems are overcome, the P76 is going to be a very good
car."
September WHEELS saw the P76 pitted against the Holden Kingswood, Falcon 500 and
Valiant in a four-car comparison of family models in the $3200-$3400 price range. The
summary at the end was fairly non-committal, but a tally of category results showed the
P76 generally in front with the Kingswood next best.
The P76 did about 6.8 km/l while the others all did about 5.3. It had the best brakes
and its gearbox was judged the best. It came first for driver position, seat design and
general accommodation, with by far the best boot. It was the best equipped of the four. In
noise level it came second to the Falcon. For finish, the Kingswood came first with the
P76 last. Door fit and trim still weren't up to scratch. The Kingswood also beat it on
handling and ride.
British Leyland showed a P76 to the British motoring press, who thought it was awfully
big for a family car. Nonetheless, it was reported Leyland Australia had arranged to sell
3500 of them to the parent company, who'd market them as a prestige model above the Rover
range.
Meanwhile, with the P76 sorted out, Leyland Australia's engineers set about extending
their own company's range. There were plans for a P76 station wagon, a P76-based coupe and
a new Model A developed from the earlier version replaced by the Marina. The Model A was
to be powered by the alloy V6 engine.
In November 1973, WHEELS showed sketches of the coupe planned for release next year and
the Model A V6 projected for 1975. The coupe was shorter, flatter and wider than the P76
sedans, with a lower nose and an immense rear hatch. It used the same mechanicals as the
sedans, and although there were no body panels in common, the family likeness was strong.
In January 1974, the P76 V8 was named the 1973 WHEELS Car Of The Year. "The
totally new Leyland sedan emerged as a remarkably fine motor car," the citation read.
"It is in the V8 version that it really shows its potential. It sets new standards
for medium-sized local cars in its ride/handling/road-holding compromise, it has fine
brakes, is comfortable, very roomy, practical and, with the all important V8 engine, has
excellent performance and superior fuel consumption compared to the V8 opposition and the
larger competitive sixes. Of course, the car is not perfect but in reaching its design
objectives the P76 V8 has contributed to the engineering standards of Australian
cars."
Local content in the P76 was close to 100 per cent. The public were more attracted by
the up-market version than Leyland had expected, and more than half the cars being
produced were V8s. However, an article in the same issue listed delays in delivery due to
industrial unrest, power strikes and a steel shortage. Leyland was still building cars,
but most had to be stockpiled because there were no parts to complete them.
The P76 had a brief competition career. Evan Green drove one in the 1974 World Cup
Rally and made the fastest time around the leg in Sicily. This included part of the former
Targa Florio course (WHEELS, September '82), so Leyland introduced a limited run of 300
P76 Targa Florios to celebrate. They all had side flashes, power steering, alloy w heels,
radial tyres, four-speed manual transmissions and limited-slip diffs.
The Leyland coupe neared production and in August 1974 WHEELS gave it a cover stony.
The basic version w as to be called the Force 7, with a six-cylinder engine. Next w as the
V8-powered Force 7V. Top of the line was to be the V8 Tour de Force, with luxury trim and
fittings. The report praised the clean lines of the tail, the room inside and the
convenience of the big hatch.
So far, Leyland Australia's campaign had gone ahead more or less on schedule. It was
like an invasion of a defended enemy coast. Plans had been laid carefully, an assault
force had been assembled and the first wave of troops had stormed ashore and won a
foothold. It was time to push on up from the beaches and capture some of the high ground.
The P76 had had a very good reception. About 2000 had been ordered in the first week
and soon there was a 1 6-week waiting list. but this w as a measure of demand, not sales.
There was a shortage of cars for dealers, particularly V8s. The P76 was slow to get on the
road in any significant numbers.
Then the cars sold had teething trouble. The V8 engine was an oil-eater until it was
properly run in and, coupled with a poor standard of finish, this earned all P7fis a
reputation for unreliability. Adherents of the rival makes fastened on this to feed a
whispering campaign.
Strikes and power cuts delayed production. One stroke of bad luck was a breakdown in
the V8 engineering shop, so that engine production for a month was down to eight a day.
All this combined to rob Leyland of the initiative. Although the first onslaught had been
a striking success, there were no reinforcements to follow up. Meanwhile, the enemy were
counter-attacking against the beach-head.
Not all of this was clear at the time. Put it was obvious Leyland was in trouble with
the new range and it was at least very likely that the parent company in England was
having second thoughts about it. One bad sign was the resignation of David Beech, the
father of the P76, in the middle of 1974. About 1000 Leyland employees were sacked and
soon afterwards Leyland
David Abell's scorched earth policy destroyed most
records concerning the P76
Australia's managing director, Peter North, suddenly resigned. too.
North said he was quitting he cause he couldn't see eye to eye with British Leyland's
management, The differences have reached a point where l feel I must resign in the
interests of the company, its employees and dealers." he said.
North, an. Australian, was succeeded by David Abell, a .31-year-old British whiz kid.
In an interview with a WHEELS reporter, Abell said the P76 program wasn't one of the
points of disagreement with Peter North. However, he didn't say how long the program could
continue. He did say he'd promised that Leyland Australia would be profitable again within
two years.
"on his record Abell has shown greater skill at pruning dead wood than he has at
manufacturing innovations," the WHEEI.S man noted. "His technical and patriotic
bias may be neatly underlined when the government gives its verdict on the Industries
Commission report. It would suit Lord Stokes and his emissary if the Federal Government
told them: Stop manufacturing and concentrate on your imports instead."
That appeared in No-ember 1974. As it turned out, David Abell didn't wait for the
Commonwealth to sort out a new motor industry policy. Before the WHEELS story was in print
he'd axed the P76 and all other machinery under development. The big Leyland plant at
Zetland in Sydney was to be sold to the government. The Marina was axed and local
production was limited to the Mini and Moke.
"I've always thought we should never have built the P76," Abell said. He told
reporters Leyland would return to profitability by concentrating on selling more Jaguars,
Rovers and Triumphs.
Leyland Australia had jumped before it was pushed. Actually, the push never came. The
Industries Assistance Commission suggested cutting the four local manufactured back to
three and when the P76 was axed Gough Whitlam called it a dud and Bill Hayden called it a
lemon. Put hen the Labor government finally brought forth its policy, local car
makers were protected by a higher tariff wall linked to a local content rule which the P76
cleared by a mile.
But in the meantime, Leyland's production lines had closed down, the last Mokes and
Marinas were being sold off at a discounts, all but a handful of the 50-odd Force 7s were
stripped and crushed for scrap and the sole P76 station wagon was left to serve as a
factory hack. In October 1974, David Abell had said about 2600 Leyland Workers would lose
their jobs, buy mid-l975, more than twice that many had been sacked.
WHEELS staff got hold of a completed Force 7 for a rushed road test. The opening spread
photo showed it parked in a churchyard. It turned out to be a roomy, impressive car, fast
enough and comfortable to drive, sporty, although not a sports car. In the market it might
have wiped the floor with the gross, hulking 'muscle car' collapse the rival makes were
offering then. 'What a bloody shame!' the heading said.
About 16,000 P 7 6s were made. Nobody really knows the exact number. As part of Mr
Abell's scorched earth policy, most of the records were destroyed. Perhaps the
13ritish management was right and it was a bad idea to start with. It was certainly
unlucky to start developing a fairly large car just before the 70s oil price rises
encouraged the big-car market to shrink.
But even if that's so, it was a bad idea w ell-executed. It was an excellent and
ingenious design. It was the most thoroughly Australian car, in concept and in content,
ever offered to the Australian public. Those issues don't cut ice with businessmen,
though. The point is, was it the car that could have taken Leyland Australia round the
corner to profitability? In the small hours of the morning, does David Abell ever lie
awake with second thoughts? From the look of him, I'd guess he doesn't . . . |